What
is Business Process Engineering?

Business Process
Engineering is "the analysis and design of
workflows and processes within and between
organizations" (Davenport & Short 1990).
Teng et al. (1994) defines Business Process
Engineering as "the critical analysis and
radical redesign of existing business
processes to achieve breakthrough
improvements in performance measures.
What does Business Process Engineering do?
- Identify and solve
process related problems including
- excessive
non-value-added time
- long lead-time
- high cost
- customer
complaints
- overproduction
- excessive
inventory
- unnecessary
capital investment
- Drive continuous
improvements and sustain cost savings.
- Enforce
based-on-the-fact quality attitude and
problem solving techniques.
QIT's Approach
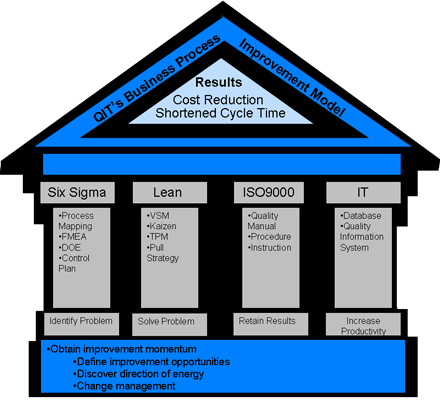
The graphic
on the left illustrates the basic model of
QIT's Business Process Engineering approach.
Phase I: Build a
foundation to obtain improvement momentum -
Research and our own experience in business
process improvement proved that many
business process re-engineering initiatives
fail because the majority in the
organization reluctant to make changes. And
most of the time, people's unwillingness
stems from lacking of communication.
Our solution
utilize a data-based feedback and system
feedback approach to have the people in the
organization to identify the improvement
opportunity and to harmonized the directions
of improvement energy. Tools from
Organization Development and Change
Management will be used to facilitate the
communications.
Phase II: Define
improvement opportunities-
once the foundation is established, use Six
Sigma tools and methodologies to define and
quantify the problems and prioritize the
objectives. Tools from Six Sigma will be
adopted to guide the analysis.
Phase III:
Design/Redesign processes and business
models - based on the
quantitative data and objectives
defined in the second phase, use Lean
concepts such as Value Stream Mapping and
Pull strategy to optimize the current
processes. Tools from Lean took kits will be
applied to design the new processes.
Phase IV:
Experiment and improve - in this
phases, use Kaizen methodology from
Lean tool kits to test and facilitate the
deployment of the new designs. In the mean
time, also apply Six Sigma methodology
to monitor and verify the results, and
fine-tune the designs. Six Sigma and Lean
tools will persist in the experiments and
the continuous improvements.
Phase V:
Fully deployment of the best practices and
retain the results - use
"say what you do and do what you say"
concept from ISO9000 to convert the best
practices into written procedures and
establish a routine internal audit
mechanism. ISO9000 standard and document
structures will be used to formalize the
best practices.
Phase VI:
New information technologies to automate
process and data processing to
increase productivity.
Key Benefits:
The bottom line, the
business enjoys the significant cost
reductions, shortened cycle time, and an
inside-out positive energy to push the
continuous improvements.
QIT Solutions
Share in LinkedIn
|